Addibond™粘接促进剂通过在金属表面形成共价键从而最大限度的提高金属与胶粘剂或者涂层的粘接,从而大大延长车身和部件的耐老化和抗腐蚀性能。
通过轻量化增加电动汽车的续航里程,用铝制造汽车的额外成本完全可以被电池组节省的成本所抵消——车身和电池系统改用铝可以将汽车的重量减轻多达 25%。并且随着轻量化的深入,越来越多的复合材料和塑料也被引入,成为汽车零部件以及发动机的重要选材之一。比如在发动机选材上,用粘合铝代替铆接钢部件以限制腐蚀。纯电动汽车发动机的整体温度水平比内燃机低,这意味着水和盐雾在零件上停留的时间更长,并可能导致腐蚀。
Addibond™是一类包含两个以上活性官能团的聚合物,能够通过反应性基团在金属基材表面形成一层共价键连接的纳米沉积层,另外一组活性基团可以与胶粘剂或者涂料在固化过程中交联,从未最大限度的提高粘合剂的强度,增加涂层的附着力。基于这个智能化学结构带来的好处,可以实现金属-胶粘剂-金属,金属-胶粘剂-塑料/复合材料的粘接,从而实现各种结构件以及非结构件的设计灵活性。
金属-胶粘剂-塑料、复合材料的典型应用在汽车部件中,比如横梁CCB,车载充电机等部件。
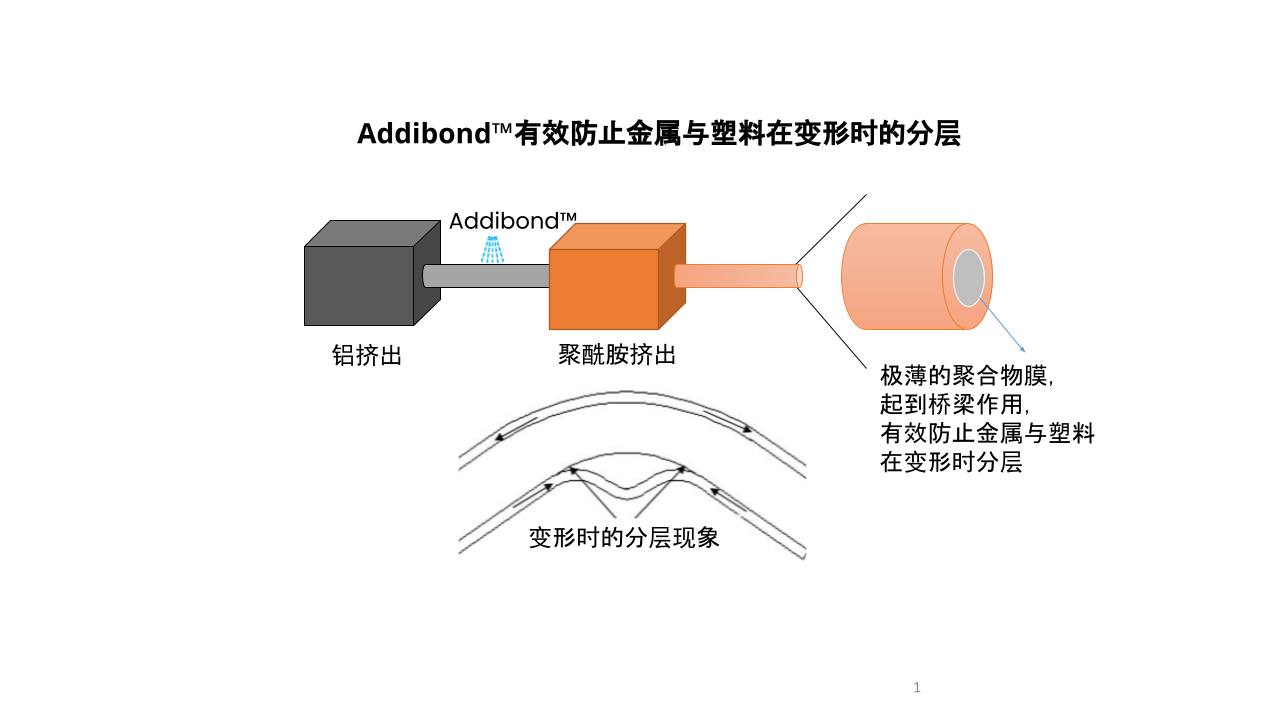
金属-胶粘剂-金属的典型应用,全铝车身粘接铝板表面处理技术有效提高全铝车身结构粘合的耐久性,允许在车辆中用铝代替钢,减少对环境的影响,减轻能源消耗,提高汽车的回收利用。
在不影响车辆安全性和舒适性的情况下,轻量化比以往任何时候都是解决这一挑战的主要手段,以提高车辆的燃油和能源效率,轻金属合金和通过粘合剂粘合消除机械紧固件的趋势越来越明显。这就需要提高金属与金属之间粘合的可靠性,为此,适当的表面处理是关键。
Addibond技术,供铝制造商使用该技术来加工汽车行业的铝卷。然后将铝卷送给汽车制造商,经过冲压成型,然后粘合形成所谓的“白色车身”。
Addibond™-聚合物通过结合两种官能团,在粘接应用中最大限度地提高粘合剂的强度,并且效性在与现有技术的综合试验中得到了验证。福特粘结应力耐久性试验(APGE)被用来评估样品在同时压缩载荷和腐蚀应力下的粘结强度,而单圈剪切(SLS)试验则用于确定在乙酸盐雾、高温和潮湿条件下进行大量循环后的内聚破坏(所需)和粘附破坏(要避免)(SWAAT - ASTM G85 A3)。
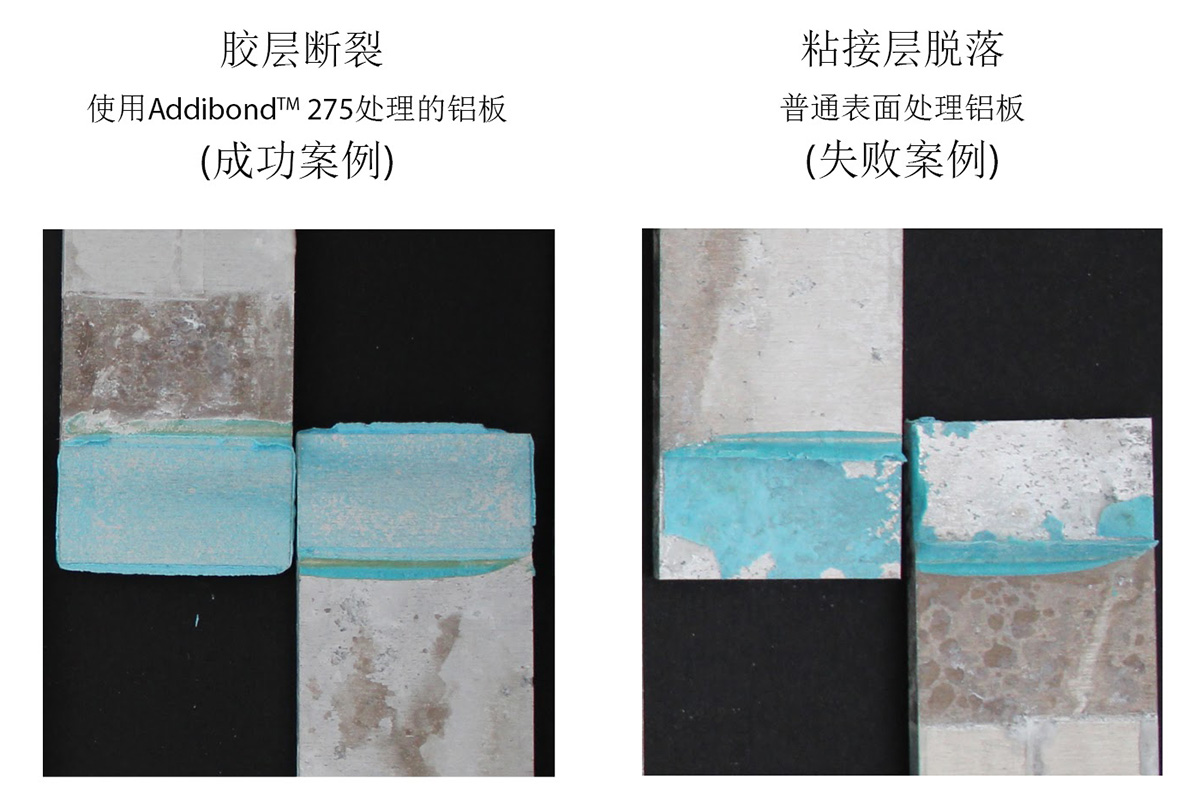
一系列的APGE/SLS结果清楚地证明,Addibond™-聚合物可以成为一个有效的推动者,在更广泛的应用中利用铝和其他轻金属的轻量化潜力,同时在制造过程中满足更高的可持续性标准。